Risk assessment is an integral part of occupational safety. Particularly on construction sites, where there are numerous hazards, it is crucial to ensure health and safety at work.
This article provides guidelines for systematically identifying potential hazards, assessing their risks and establishing appropriate protective measures.
The most important facts in brief
✓ The risk assessment is a legally prescribed and indispensable part of occupational health and safety on construction sites in order to minimize the risk of accidents and protect health. In Germany, this obligation is based on the Occupational Health and Safety Act (ArbSchG) and the Construction Site Ordinance (BaustellV).
✓ It is a continuous process that includes the identification of hazards, the assessment of risks and the definition of protective measures, taking into account the TOP principle. Regular inspection and maintenance of work equipment and safety devices are crucial in order to identify and minimize hazards.
✓ Complete documentation and communication of the results of the risk assessment are crucial in order to strengthen the safety culture in the company and ensure compliance with legal requirements as well as preparation for possible external inspections.
The importance of risk assessment on construction sites
Risk assessment is essential on construction sites, as the construction industry is one of the sectors with the highest number of serious accidents at work. Every accident is one too many. Everything must therefore be done to prevent these avoidable incidents.
A proper risk assessment can systematically identify the risks present on a construction site. These hazards range from physical risks such as collision, crushing and falling hazards to health hazards such as respiratory and lung diseases that can be caused by contact with harmful substances. Identifying these hazards is the first step in preventing accidents and ensuring health protection.
Steps for carrying out a risk assessment
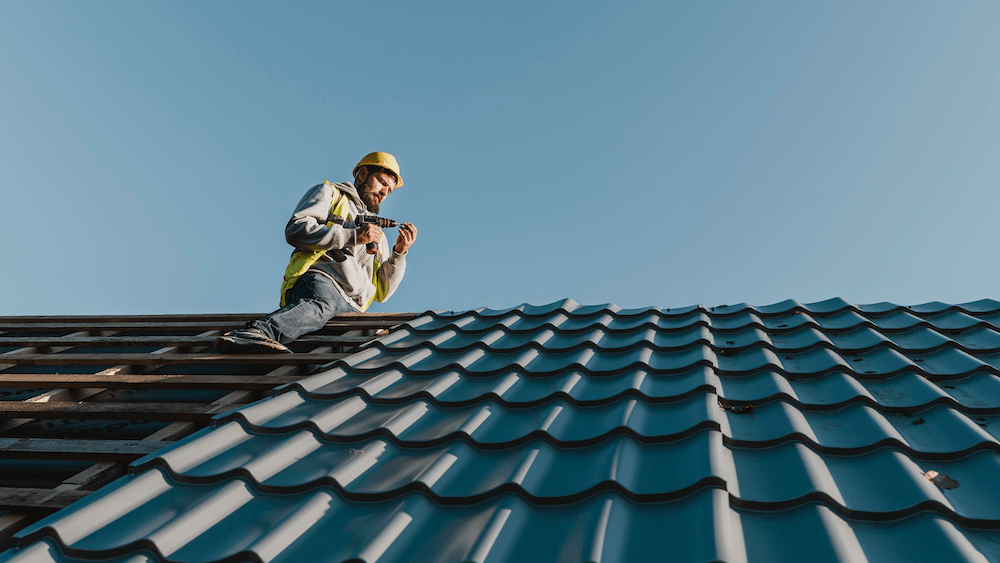
Carrying out a risk assessment is not a one-off task. It should be carried out before work begins and then taken into account throughout the planning and set-up process of the construction site. As working conditions and potential hazards can change during a project, the risk assessment must be updated regularly. It is an ongoing process that involves identifying hazards, evaluating risks and determining suitable measures.
1. select areas and activities to be assessed
The first step in the risk assessment is to identify potential hazards. To do this, an inventory is first carried out to record all work areas and activities that could be potentially hazardous. For example, existing information such as workplace descriptions, hazardous substance lists and maintenance and inspection logs for machines and systems are reviewed and evaluated.
There are various danger zones on a construction site that require special attention, such as the working area around dangerous machinery or the area where scaffolding is erected. It is crucial to take into account the specific circumstances of each construction site in order to create a practical and effective risk assessment.
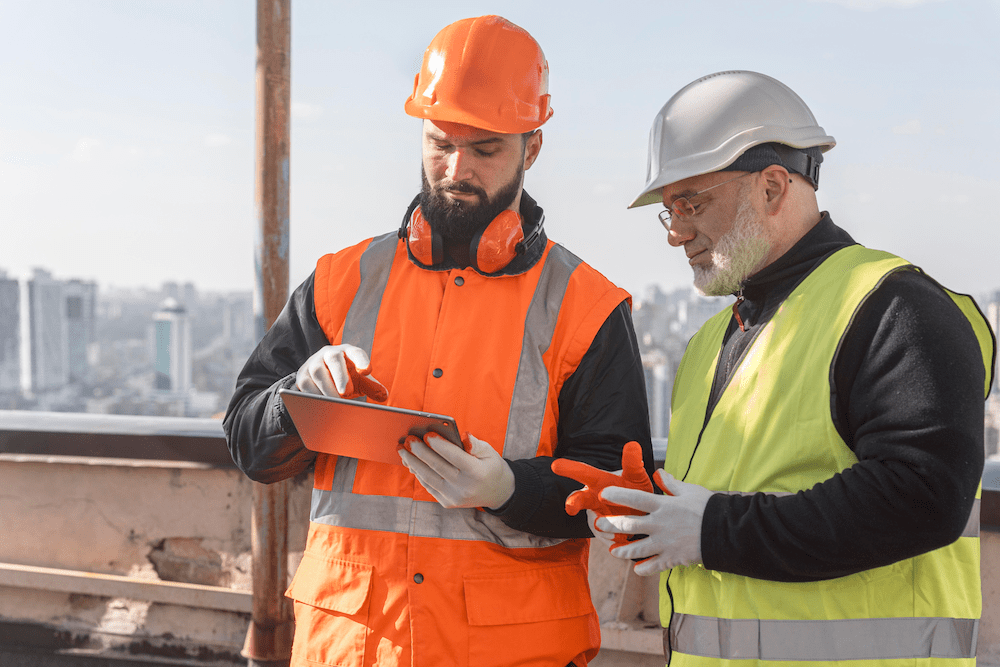
2. identify hazards and stresses
In the next step, the identified areas and activities are examined in detail for specific hazards and stresses. Hazards can be identified in different ways: through inspections, inspections of work equipment and interviews with employees.
It is important to consider both physical and mental stress. This is the only way to create a comprehensive picture of the risks on the construction site and ensure that no potential hazards are overlooked.
3. assess risk
In order to assess the risk, the first step is to check whether there are legal requirements or specific regulations that must be observed. Based on these requirements, the hazards are assigned to a specific hazard level and evaluated. If there are no specific requirements, the risk assessment is carried out by combining the severity of damage and the probability of occurrence, e.g. using a risk matrix according to Nohl.
The risk is categorized into levels in order to rate it as "very low" to "high". This makes it easier to prioritize the risks. Protective measures that have already been implemented must also be evaluated in order to check their effectiveness and make any necessary adjustments.
4. define protective measures
After the risk assessment, the next step is to define protective measures. These are prioritized according to the STOP principle:
- Substitution - replacing hazardous substances or processes with less hazardous ones.
- Technical measures - tackle hazards at source, e.g. through safeguards, protective equipment or machine maintenance.
- Organizational measures - Design work processes and organization in such a way that risks are minimized, e.g. through clear responsibilities and training.
- Personal protective measures - provision of protective equipment such as helmets, gloves, respiratory protection or personal emergency signaling devices.
The defined measures require a clear assignment of responsibilities, deadlines for implementation and the provision of the necessary resources. It is crucial that everyone involved knows exactly what is expected of them, when their tasks are to be completed and what resources must be available to effectively implement the protective measures on the construction site.
5. implement measures
The defined protective measures must be implemented consistently. To this end, responsible persons are appointed, schedules are drawn up and employees are informed about the measures. On a construction site, this can be done through safety instructions and the provision of personal protective equipment (PPE).
6. check the effectiveness of the measures
Regular checks are carried out to determine whether the measures introduced effectively reduce the risk and whether the hazards are manageable. If necessary, additional measures must be taken. On construction sites, this can be done by carrying out further safety inspections and interviewing employees.
7. documenting the risk assessment
Proper documentation of the risk assessment is just as important as its implementation. It ensures transparency and traceability. At the same time, communicating the results to employees is essential in order to successfully implement the safety measures in everyday working life.
8. instruction and communication
An effective risk assessment requires that all employees fully understand the risks and protective measures. However, time pressure, language barriers and the attitude "nothing will happen to me" often hinder the safety culture on construction sites. Therefore, instructions must be clear, multilingual and practical to ensure understanding. The cycle of negligence and risk must be broken - because every accident not only costs health, but also time and money. The primary goal remains the protection of all employees.
Legal basis and responsibilities
Occupational health and safety is not an optional luxury. It is enshrined in law and employers are obliged to carry out and document a risk assessment. This is laid down in the Occupational Health and Safety Act (ArbSchG) § 5. It is not only a question of compliance with regulations, but also a question of responsibility towards employees in the context of occupational health and safety.
In addition to the Occupational Health and Safety Act, there are also other statutory provisions that extend the obligation to carry out a risk assessment. These include
- the Workplace Ordinance (ArbStättV)
- the German Ordinance on Industrial Safety and Health (BetrSichV) in conjunction with the Technical Rules for Industrial Safety (TRBS) 1111
- DGUV Regulation 1
All of these regulations are aimed at ensuring a safe working environment on the construction site.
Action aids and checklists for risk assessment
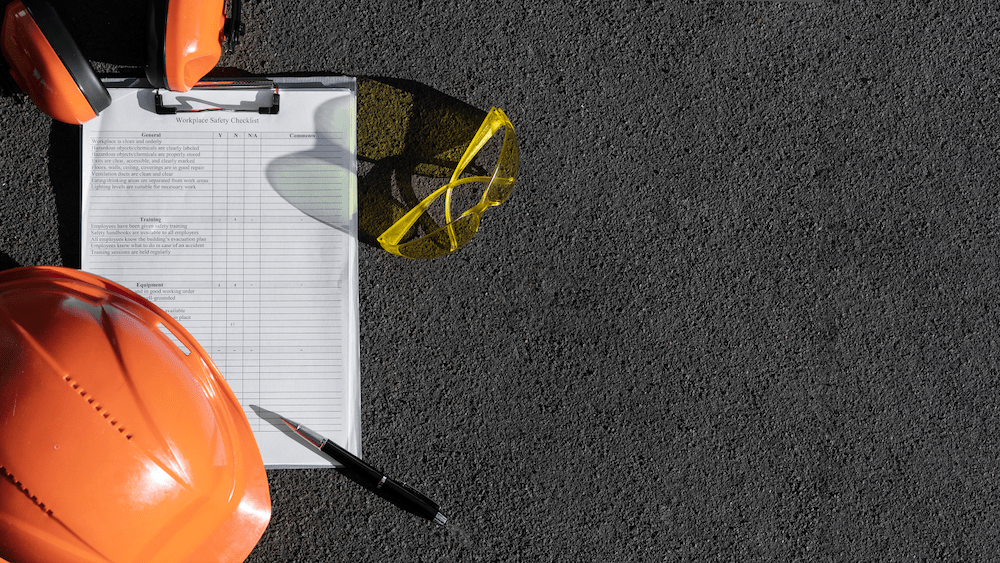
Carrying out a risk assessment can seem complex, but there is support available. Employers' liability insurance associations and accident insurance funds provide numerous aids and checklists to guide employers through the process. These templates and instructions make it possible to create practical risk assessments that can be adapted to the specific requirements of the company.
BG BAU guidelines
The BG BAU (German Social Accident Insurance Institution for the construction industry) offers valuable resources based on the quality standards of the Joint German Occupational Safety and Health Strategy (GDA). These aids support the systematic identification and assessment of hazards on construction sites.
The BG BAU also provides an app that offers practical information and occupational safety measures for the construction industry. The app is divided into various chapters and covers topics such as risk assessment, personal protective equipment, first aid, safe use of work equipment and machinery and ergonomic workplace design. Further details on the app and the individual chapters can be found at(https://www.bgbau-medien.de/app/daten/site/kapitel.htm).
Checklists for an effective assessment
Checklists are indispensable tools for recording work processes in a structured manner and ensuring that no potential sources of danger are overlooked. Especially in complex construction site processes, they help to maintain an overview and address hazards in a targeted manner.
Documentation and communication of the risk assessment
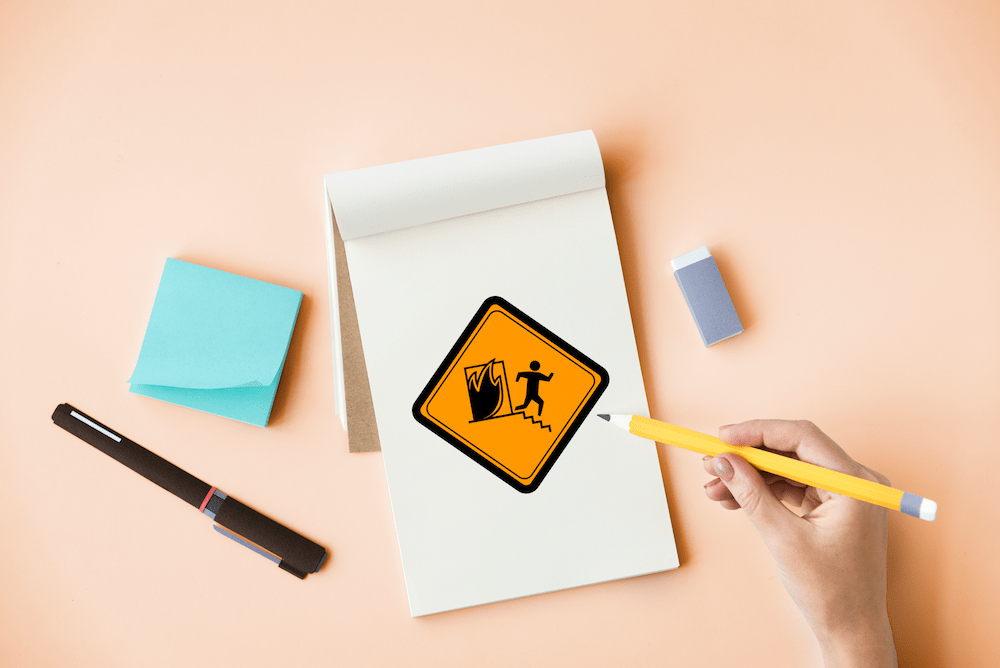
Documentation requirements
The documentation of the risk assessment must contain all relevant information in order to meet the legal requirements. This includes the results of the risk assessment, the protective measures implemented and their review. Whether in paper or digital form, it is important that the documentation meets operational requirements and is easily accessible.
Communicating the results
Employees must be informed about the hazards and protective measures. This can be done through operating instructions, meetings, written messages or notices. Clear communication promotes safety awareness and strengthens the safety culture in the company.
Conclusion
Risk assessment is a central component of occupational safety on construction sites. It enables potential risks to be identified and evaluated at an early stage and protective measures to be implemented. To ensure that this remains effective in the long term, the risk assessment must be regularly reviewed and adapted to changing conditions. This is the only way to ensure a safe working environment in the long term.
Frequently asked questions
Is a risk assessment mandatory?
Yes, the risk assessment is mandatory in accordance with the Occupational Health and Safety Act and DGUV Regulation 1 in order to ensure the safety and health of employees.
Where can I get a risk assessment?
Company doctors, occupational safety specialists and the employers' liability insurance associations offer support with risk assessment.
How does a risk assessment work?
First, the work areas and activities are defined, then the hazards are determined. This is followed by a risk assessment to determine the appropriate measures.
What is the risk assessment on construction sites?
The purpose of risk assessment on construction sites is to identify risks and take measures to ensure the health and safety of employees.
Who is responsible for carrying out a risk assessment?
The employer is legally obliged to carry out, document and continuously improve the risk assessment.
How often does a risk assessment have to be updated on the construction site?
A risk assessment should be regularly reviewed and updated, especially if the working conditions or activities change. Changes in the project phases, the use of new work equipment or the introduction of additional activities require the assessment to be adapted.
What happens if the risk assessment is not carried out correctly?
If the risk assessment is not carried out or is carried out inadequately, the employer faces fines and liability risks. In addition, the risk of accidents increases, which can lead to personal injury, loss of production and higher insurance costs.
How are risk assessment and instruction related?
The risk assessment forms the basis for all safety instructions. The identified hazards and defined protective measures must be clearly communicated to employees before they start work. This is the only way to ensure that all employees are informed about the risks and behavior and that the protective measures can be implemented effectively.