Safety in the workplace is no coincidence - it is regulated by law. The German Ordinance on Industrial Safety and Health (BetrSichV) specifies exactly how work equipment must be used and systems requiring monitoring must be operated. Its aim is to identify risks at an early stage, prevent accidents and create a working environment in which the health of employees is paramount.
The most important facts in brief
✓ The German Ordinance on Industrial Safety and Health (BetrSichV) requires a comprehensive risk assessment and the use of suitable protective measures to ensure safety in the workplace.
✓ Regular inspections and maintenance of work equipment are essential to ensure its functionality and safety.
✓ Employers are obliged to regularly instruct employees and enable them to use work equipment safely.
Basics of the Ordinance on Industrial Safety and Health (BetrSichV)
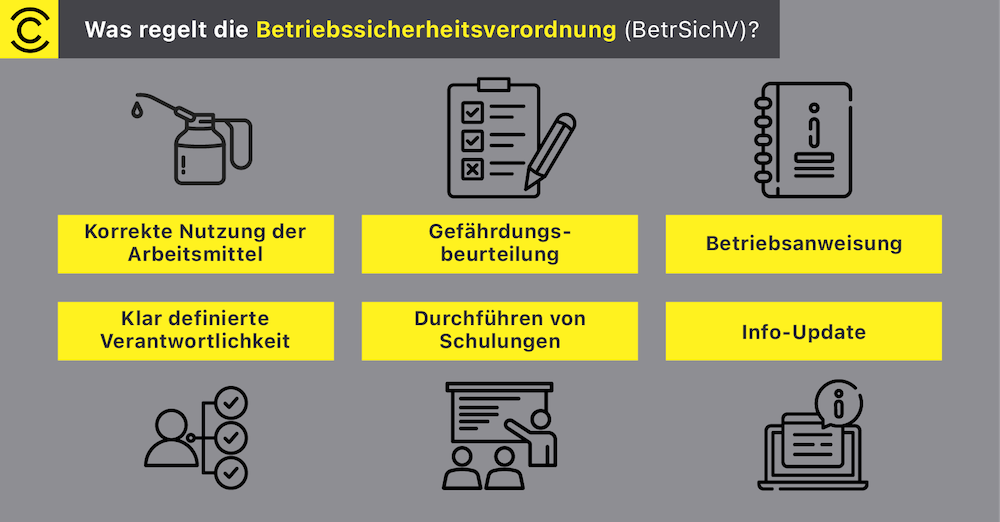
The Ordinance on Industrial Safety and Health (BetrSichV) came into force on June 1, 2015. Its main objective is to create a safe working environment by laying down requirements for the use of work equipment and the operation of systems requiring monitoring. This is of crucial importance, as the safety and health of employees are at the heart of the regulation.
The BetrSichV specifies the Occupational Health and Safety Act (ArbSchG) and is closely related to other occupational health and safety regulations such as the Hazardous Substances Ordinance (GefStoffV). While the ArbSchG provides the general legal framework, the BetrSichV specifies the requirements for the safe operation of work equipment. Coordination with other regulations is essential, especially for activities involving hazardous substances or special work processes.
The basic components of the BetrSichV include the standardized risk assessmentthe safety assessment, consideration of the state of the art and compliance with minimum requirements. These elements form the foundation of the ordinance and ensure that a high safety standard is maintained.
Another important aspect of the Ordinance on Industrial Safety and Health is the regulation of the requirements for the safe use of work equipment. This includes the selection, provision, use and maintenance of work equipment in order to ensure the safety and health protection of employees. The Ordinance on Health and Safety in the Use of Work Equipment is therefore a central component of occupational health and safety.
In addition, regular inspections must be carried out and training organized to ensure the safe use of work equipment. Employers and employees are obliged to keep up to date with new legal requirements and technical developments.
The clear definition of responsibilities also plays a major role. Employers are responsible for taking the necessary protective measures and ensuring that the specified safety standards are met. This includes both the technical equipment and the training of employees.
BetrSichV: Overview of key terms
In order to implement the Ordinance on Industrial Safety and Health correctly, it is important to understand the key terms:
Work equipment includes tools, machines, devices and systems. This also includes equipment requiring monitoring that is used at work. This definition covers a wide range of equipment used in different areas of work.
Employees are not only employees in the traditional sense, but also pupils, students and other persons who use work equipment. This shows that the regulation offers comprehensive protection for all persons who come into contact with work equipment in any form. The implementation of this regulation is crucial for the protection of all those involved.
A competent person is someone who has the necessary knowledge and experience to carry out specific tasks safely. These persons play an important role in the maintenance and inspection of work equipment. Maintenance itself includes all measures to maintain or restore the safety of work equipment.
Inspections are another central concept of the regulation. They include the assessment of whether the current state of work equipment meets the safety requirements. A change requiring inspection refers to any measure that could affect the safety of work equipment and therefore requires a new inspection.
Risk assessment and protective measures
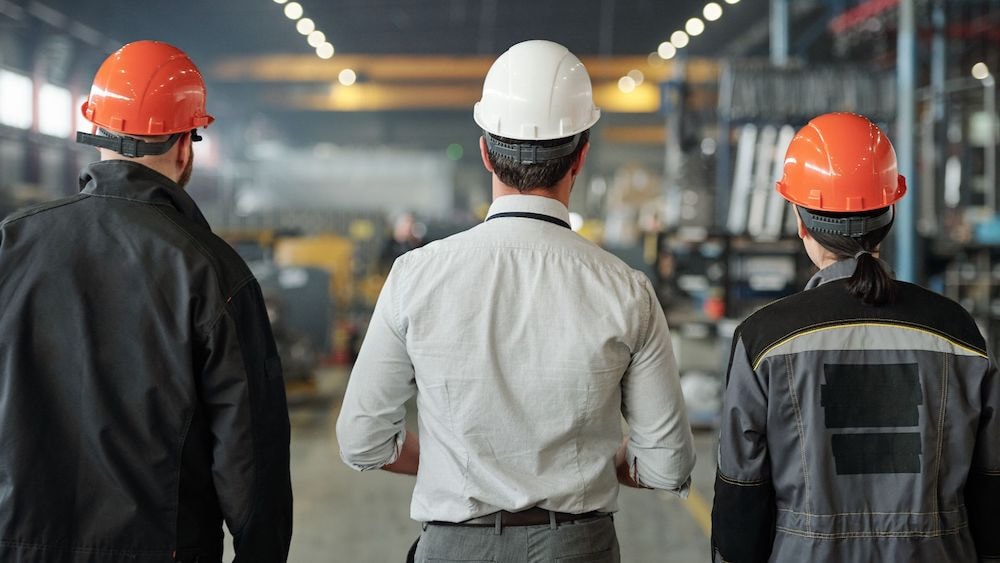
Risk assessment is a central element of the German Ordinance on Industrial Safety and Health. Employers are obliged to assess all possible risks before using work equipment. This assessment must begin before the work equipment is selected and purchased and must be updated regularly, especially if working conditions change.
All hazards that may arise when using work equipment must be taken into account in the risk assessment. The employer must ensure that the assessment is documented. This is an important step in ensuring the safety and health of employees.
Suitable protective measures must be taken on the basis of the risk assessment. According to the TOP principle, these measures can be of a technical, organizational or personal nature and must minimize or completely eliminate the risks. Even the CE marking of a piece of work equipment does not release it from the obligation to carry out a risk assessment. The CE marking indicates that the work equipment complies with basic EU directives - in particular the Machinery Directive. However, it does not replace an operational risk assessment. Employers must assess on their own responsibility whether the respective work equipment can be operated safely in the specific application. This includes, in particular, changes to the environment or the intended use.
Written operating instructions must be made available to employees in a comprehensible form before they use work equipment. This helps to ensure that all employees are informed about the potential hazards and the necessary protective measures.
In summary, it can be said that the risk assessment and the protective measures derived from it are essential components of the Ordinance on Industrial Safety and Health. They ensure that the safety and health of employees is guaranteed when using work equipment.
Technical protective measures and safety precautions in accordance with the Ordinance on Industrial Safety and Health
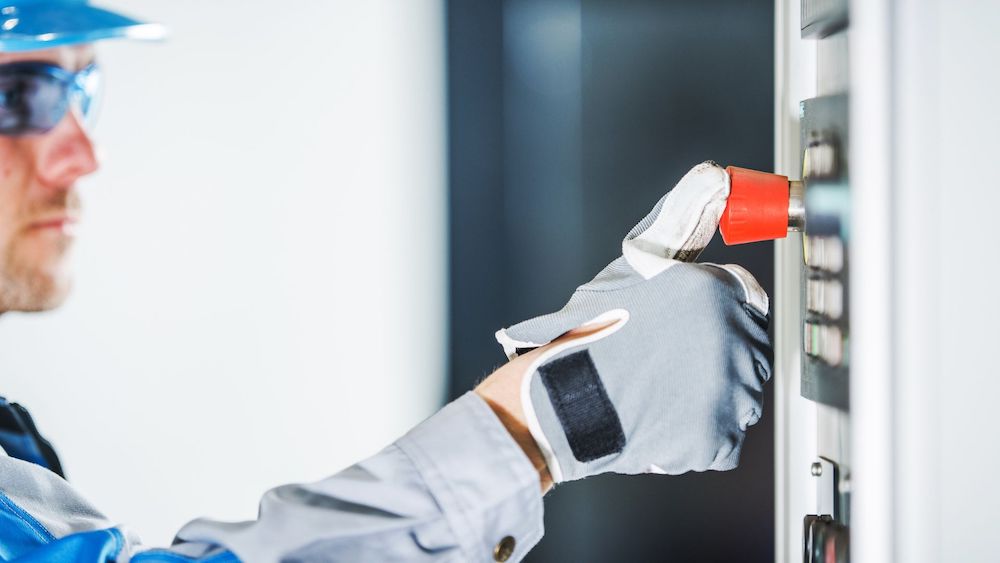
Technical protective measures and safety precautions are of central importance to ensure the safety of employees. One of the most important measures is the ergonomic design of work equipment, which takes into account the physical characteristics and abilities of employees. This helps to minimize physical strain and health risks.
When using work equipment outdoors, safety standards must be adhered to regardless of the weather conditions. This ensures that the safety of employees is guaranteed even under difficult conditions. Safety equipment must be functional and must not be tampered with in order to ensure the safety of employees.
In accordance with the TOP principle, which is regulated in the Industrial Safety Regulation in §4 - Paragraph 2, technical measures are prioritized over organizational and personal measures. Technical measures should eliminate hazards directly at their source. These include
- Automatic shutdowns:
Sensors or circuits that automatically stop machines in the event of danger. - Protective covers:
Fixed or movable barriers that cover dangerous machine parts. - Emergency stop switch:
Manually operated switches that stop machines immediately to prevent accidents. - Dead man's switch:
Safety device that stops machines when the operator no longer actively intervenes. - Extraction devices:
Technical systems that extract pollutants from the air and clean the room air. - PNA (Personal emergency signal systems):
Devices that automatically trigger an alarm when the employee is in distress while working alone.
Orientation through technical rules for operational safety (TRBS)
The Technical Rules for Industrial Safety (TRBS) are used for the practical implementation of the requirements of the Industrial Safety Regulation. They specify the legal requirements, taking into account the state of the art, occupational medicine and hygiene. By applying them, it is assumed that the requirements of the BetrSichV are fulfilled - which significantly increases legal certainty in the company.
Important examples of TRBS:
- TRBS 1111 - Risk assessment: Provides methodical instructions for implementation and documentation.
- TRBS 1201 - Testing of work equipment: Regulates the type, scope, deadlines and qualification of inspection personnel.
- TRBS 1115 Part 1 - OT safety of technical control systems: Addresses the protection of safety-relevant control systems against digital attacks for the first time. Particularly relevant for companies with automated systems and networked operational technology.
Note: The TRBS not only supplement the BetrSichV technically, but are also increasingly building a bridge to topics such as cybersecurity in occupational health and safety - a growing risk due to increasing digitalization in companies.
Regular inspection and maintenance of work equipment
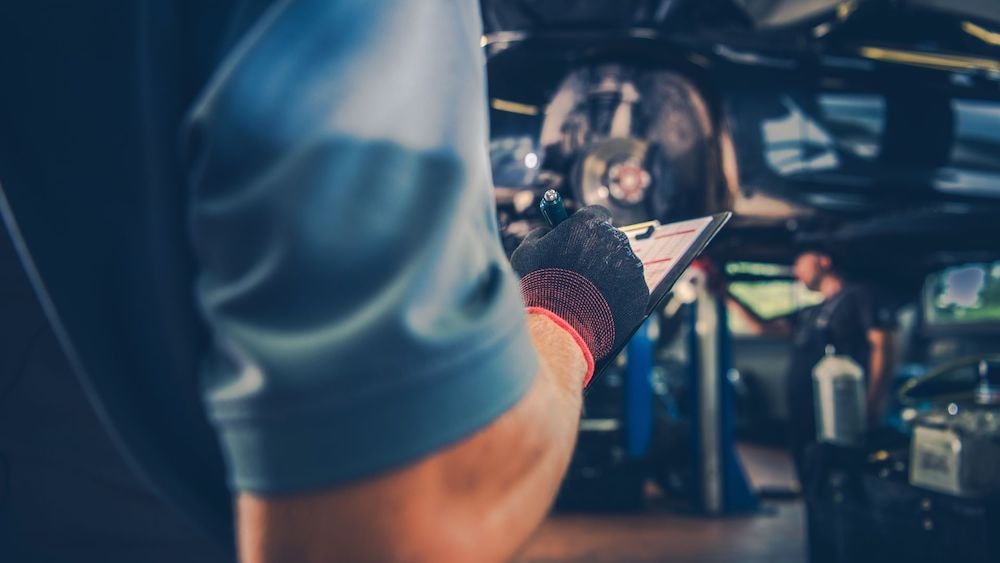
Regular inspections and maintenance are essential to ensure the safety and functionality of work equipment. These inspections must be carried out by qualified persons who have the necessary specialist knowledge. The employer is responsible for the proper performance and documentation of all required inspections.
Maintenance includes all measures required to maintain or restore the safe condition of work equipment. This also includes regular inspection and maintenance to ensure that the work equipment permanently meets the required safety standards.
Violations of the obligations of the BetrSichV can be punished with severe fines in accordance with §22 BetrSichV - for example in the event of a missing or inadequate risk assessment, failure to carry out inspections or the operation of unsafe work equipment. In the event of intentional or negligent hazards, there may also be criminal consequences (§26 ArbSchG).
Documentation of the tests is crucial in order to prove compliance with safety standards. Employers must ensure that the safety and protective distances are observed during the assembly and dismantling, testing and maintenance of work equipment. This also applies to systems requiring monitoring.
Old machine safety according to DGUV regulation 100-500
For many companies, the question arises as to what applies to older machines and tools that were purchased before the Ordinance on Industrial Safety and Health (BetrSichV) came into force in 2002. The answer can be found in §7 Para. 2 of the BetrSichV: The regulations that were valid at the time of initial commissioning apply to these so-called "old stocks".
As many old accident prevention regulations have since been repealed, DGUV Rule 100-500 (formerly BGR 500) is a practical collection that preserves the core content of these regulations. It is divided into work equipment (e.g. drills, cranes, presses) and work processes (e.g. welding, lifting, transportation) and contains specific requirements for operation, testing, maintenance and protective measures - especially for older machines. Although it is not legally binding, it is used by many companies as a recognized guide to fulfilling the objectives of the BetrSichV.
Special operating conditions and accidents
Special operating conditions and accidents require specific measures to ensure the safety of employees. Employers must take measures to prevent unstable operating conditions of equipment. This is particularly important in order to avoid accidents and malfunctions.
Safety measures for working in hazardous areas are essential, especially during the setup and testing of equipment. In the event of an emergency, effective escape routes must be set up to enable the immediate assistance of employees. Warning devices are required to provide information about hazards resulting from particular operating conditions or malfunctions.
The danger zone is the area in which the health of employees can be endangered by the use of work equipment. It is therefore important that all necessary measures are taken to ensure safety in these areas.
Instruction and special assignment of employees
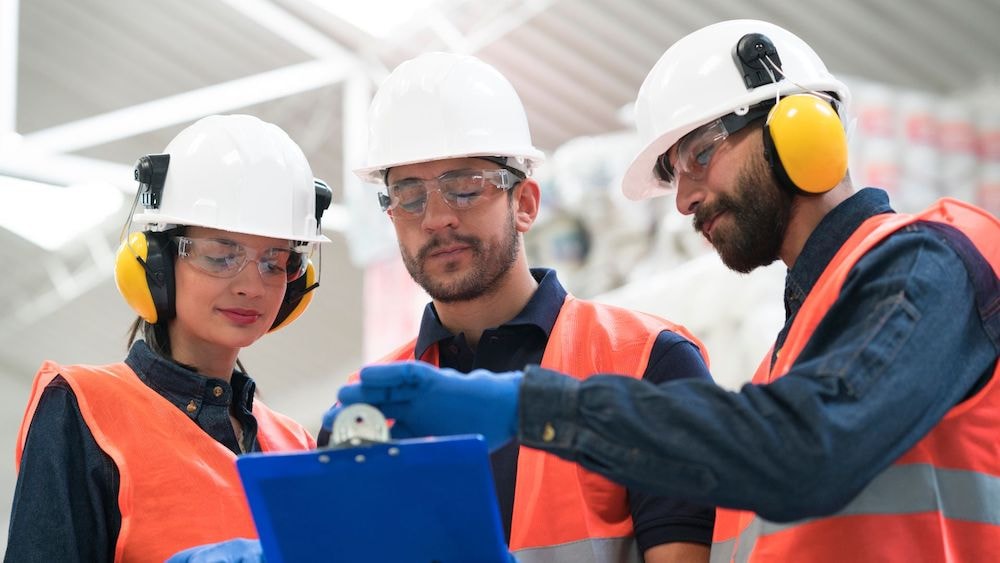
The training and instruction of employees is an essential part of the Ordinance on Industrial Safety and Health. The employer is obliged to regularly instruct employees in the safe use of work equipment. This ensures that employees have the necessary knowledge to use the work equipment safely.
Providing the necessary information and training is crucial for safety in the workplace. This also includes training employees in emergency situations by simulating practical scenarios. As a result, employees are better prepared for potentially dangerous situations and can act accordingly.
Cooperation between different employers
When multiple employers operate in the same workplace, their cooperation is essential to ensure workplace safety. They must provide emergency services with the necessary information on potential hazards and precautionary measures to create an effective link. This is particularly important in order to be able to react quickly and effectively in an emergency.
Coordination between the various employers is essential to ensure safety in the workplace, especially in the event of increased risks. In order to optimize cooperation, coordinators should be appointed to organize the exchange of information between employers and ensure that protective measures are coordinated. This prevents additional hazards arising from uncoordinated work.
An example: an electrical company and a scaffolding company are working on a construction site at the same time. To ensure that the electricians are not endangered when working on cables because scaffolding is being erected above them, both companies must coordinate their work in terms of timing and organization.
Conclusion
The German Ordinance on Industrial Safety and Health (BetrSichV) is a comprehensive set of regulations that ensures the safety and health of employees in the company. With clear specifications and comprehensive regulations, it ensures that work equipment is used safely and hazards are minimized. Employers are obliged to carry out risk assessments and take suitable protective measures to ensure the safety of employees.
Technical protective measures and safety precautions are of central importance to ensure the safety of employees. Regular inspections and maintenance are essential to ensure the safety and functionality of work equipment. Special operating conditions and accidents require specific measures to ensure the safety of employees. Training and instruction of employees are an essential part of the Industrial Safety Regulation, as is cooperation between different employers to ensure safety in the workplace.
Frequently asked questions
What is the main objective of the Ordinance on Industrial Safety and Health (BetrSichV)?
The main objective of the German Ordinance on Industrial Safety and Health (BetrSichV) is to create a safe working environment by ensuring the safety and health of employees when using work equipment.
Who is affected by the Ordinance on Industrial Safety and Health?
The Ordinance on Industrial Safety and Health applies to all companies that use work equipment such as tools, machines and systems that require monitoring. The only exceptions are companies that are subject to the Federal Mining Act, unless they also operate systems that require monitoring.
What is a risk assessment?
A risk assessment is the systematic evaluation of risks in the workplace. It should be carried out before work equipment is procured and updated regularly to ensure appropriate protective measures are taken.
Which technical protective measures are important for the safety of employees?
Important technical measures include, for example, the installation and regular testing of functional protective equipment such as emergency stop switches, protective covers or dead man's switches. Automatic shutdowns, extraction devices and the ergonomic design of workstations are also included. The aim of technical protective measures is to minimize physical and health risks for employees.