In accordance with Section 5 of the Occupational Health and Safety Act, every employer must determine the hazards for lone workers by means of a risk assessment and evaluate the working conditions.
Suitable measures are determined on the basis of the assessment and documented in accordance with §6 of the Occupational Health and Safety Act.
The risk assessment for lone working consists of the hazard identification and the risk assessment. The latter is carried out separately for each identified risk factor.
The most important facts in brief
✓ The employer is obliged to carry out a risk assessment for lone workers
. This includes determining the hazards in the workplace and assessing the working conditions.
✓ Risk assessment in the workplace requires the cooperation of various stakeholders, such as the occupational safety specialist and the company doctor.
✓ The risk assessment is carried out after the hazard assessment and takes into account the hazard level (GZ), the probability of an emergency (NW) and the time until the start of emergency measures (EV).
What is lone working and why is a risk assessment necessary?
Lone working refers to any activity that is carried out outside the call and sight range of other people. This means that the person working alone cannot receive immediate support from colleagues or superiors in the event of an emergency. A risk assessment is mandatory for lone working, as it forms the basis for determining the risks associated with lone working.
The risk assessment is required to identify the specific hazards to which people working alone could be exposed. These include physical risks such as accidents or injuries, as well as mental strain due to isolation or stress. By systematically analyzing these risks, suitable protective measures can be developed and implemented to ensure the safety and health of employees.
A key aspect of the risk assessment for lone working is taking into account the time required to provide assistance in an emergency. As the person working alone is working out of call and sight of others, measures must be taken to ensure that help can be provided quickly and effectively in an emergency. This can be achieved through technical solutions such as personal emergency signal systems or organizational measures such as regular check-up calls.
Basics of risk assessment in the workplace

The basis for the risk assessment is a previous site inspection, during which all areas of the company and the individual workplaces contained therein are taken into account. In addition to the occupational safety specialist, the company doctor, representatives of the works council and safety officers are usually involved in this process. Depending on individual discretion, however, owners, managing directors, supervisors and selected employees can also take part in the inspection.
Hazards can arise in particular from...
- the design and furnishing of the workplace and the workplace
- physical, chemical and biological effects, for example when working in the laboratory
- the design, selection and use of work equipment, machines, devices and systems, for example in the construction industry
- the organization of work and production processes, workflows and working hours
- Inadequate qualification and instruction of employees
The risk assessment takes place after the hazard identification. This is determined on the basis of the hazard level (GZ), the emergency probability (NW) and the time until the start of emergency measures (EV) . It should be noted that this type of risk assessment focuses in particular on individual workplaces or lone working. Other methods, such as the Nohl risk matrix, are suitable for general risk assessment.
Hazard level (GZ)
The hazard level (GZ) is determined on the basis of the hazard factors.
Emergency probability (NW)
The indicator (NW) is determined on the basis of the probability of an emergency. It takes into account various factors that could influence the likelihood of a potential emergency in the workplace.
This includes aspects such as the type of activities that are carried out, the environment in which work is carried out and the safety measures in place.
The NW assesses the possibility that an emergency could occur during the performance of work, be it a medical emergency, an accident or any other sudden and unexpected situation that requires an immediate response.
This probability is then used to determine the key figure for the emergency probability in order to complete the risk assessment as part of the hazard assessment and to take appropriate protective measures.
Primary care (PA)
The EV is determined based on the time between the alarm being triggered and the start of assistance on site. This time period is taken into account to determine how quickly first responders or emergency services can reach the scene of the incident to begin first aid measures or other supporting actions.
It plays a crucial role in assessing the efficiency and speed with which help arrives on site to assist in an emergency or unforeseen situation.
If it takes more than 15 minutes to start rescue operations, the effectiveness of the rescue chain is not guaranteed. In such cases, lone working is not permitted.
A longer period of time could mean that the relief efforts are not efficient enough to be on site quickly enough to provide appropriate support. In such cases, where the initial response time is too long, it is not considered safe to work alone and alternative safety precautions must be taken to ensure the safety of workers.
Risk assessment for the workplace
The classification into hazard levels (GZ) already results in the following measures for the lone worker workplace.
The following calculation is performed for the final assessment of the risk:
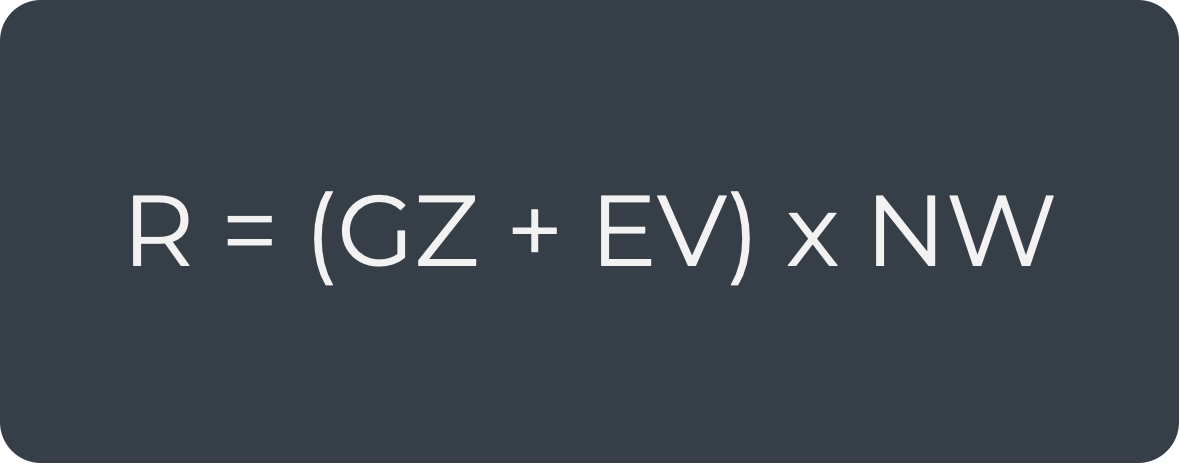
If R is less than 30, then the risk is acceptable and no further measures need to be taken.
If R is greater than 30, this is referred to as a hazardous case.
This means that technical, organizational or personnel measures must be provided to minimize risk so that the GZ or NW factor is reliably reduced.
Sensible technical measures include, in particular, the use of emergency call and monitoring options for people working alone, for example through a digital emergency system such as CALIMA.
7 Action steps for risk assessment
The risk assessment steps are essential to ensure a safe working environment:
1. recording the company organization
First, the company structure is analyzed. All relevant departments, work areas and responsibilities are recorded. Who is responsible for which processes? What interfaces are there between the individual areas? A clear organizational overview makes it possible to identify potential sources of danger at a structural level and derive targeted measures.
2. recording the activities
In this step, all relevant work processes and tasks are documented in detail. This includes routine activities as well as special or unusual work processes. This analysis helps to identify specific hazards for individual activities and derive suitable protective measures.
3. determine possible hazards
In this step, all potential sources of danger are systematically analyzed in order to identify risks at an early stage and develop suitable protective measures. Both physical hazards (e.g. from machines, tools, working materials, noise, unergonomic working conditions or a lack of protective equipment) and mental stress (e.g. from high work pressure, monotonous activities, unclear work requirements or poor work organization) are considered.
4. assessing the risk
The identified hazards are assessed in terms of their severity and probability in order to determine the risk to employees. This helps to prioritize the risks and determine the urgency of protective measures.
5. definition of protection targets and measures
Specific protection targets are defined based on the risk assessment. Measures are defined to reduce or eliminate risks in order to minimize hazards and create a safe working environment.
6. realization of the measures
The planned protective measures are implemented. This may include providing appropriate protective equipment, offering employee training or making adjustments to work processes in accordance with the defined protection goals.
7. monitoring the effectiveness and updating the risk assessment
A regular review is carried out to determine whether the measures introduced are having the desired effect. If necessary, adjustments are made to ensure that the safety precautions are effective and guarantee a safe working environment. These checks and adjustments are crucial in order to continuously improve occupational health and safety and keep it up to date.
The employer is obliged to review and update the risk assessment regularly every two to three years or if there is an occasion, e.g. introduction of new machinery, work processes or activities.
Is the risk assessment legally binding?
Yes, the risk assessment is mandatory by law. In accordance with the Occupational Health and Safety Act and DGUV Regulation 1, the employer is responsible for the safety and health of employees in the workplace.
It is the employer's duty to ensure a safe workplace. The risk assessment is the central instrument for implementing this obligation. It can either be carried out directly by the employer or by experts who are commissioned to do so.
However, the legal responsibility for carrying out and monitoring the risk assessment always lies with the employer, even if they delegate the task. It is important that the employer ensures that the assessment is carried out and monitored properly in order to meet the legal requirements.
You can find out more here.
Risk assessment - template
To support the implementation of risk assessments in accordance with the Occupational Health and Safety Act (§§ 5 and 6), the German Social Accident Insurance Institution for the woodworking and metalworking industries (BGHM) provides templates for risk assessments in Word and PDF format for download, as well as the option of an online risk assessment.
This is available for various industries, including:
- Construction sites / assembly
- Wood / plastics / model making
- Vehicle maintenance
- Mechanical engineering
- Sanitary / heating / air conditioning
- Metal
- Surface treatment
You can also use our sample instructions for risk assessment as a guide.
What role does the TOP principle play in risk assessment?
The TOP principle is a hierarchy for security measures that classifies technical, organizational and personal protective measures according to their priority.
The TOP principle is of crucial importance in the risk assessment process in order to ensure safety in the workplace. This process is divided into several phases:
At the beginning of the risk assessment, all possible sources of danger and risks in the workplace are identified. This is done through observations, analysis of work processes and discussions with employees.
In the next step, the identified hazards are evaluated in order to assess their severity and probability. A distinction is made as to whether they can be eliminated or reduced by technical, organizational or personal measures.
The TOP principle is then applied:
1. technical measures (T):
First, technical solutions are considered to eliminate or reduce the hazards at their source.
Technical protective measures refer to changes to work equipment, machines, work processes or the working environment in order to reduce or eliminate hazards. They aim to eliminate the hazards directly at their source.
These measures could include protective devices on machines, the adaptation of work equipment or the design of the workplace.
2. organizational measures (O):
If technical solutions are not sufficient or not possible, organizational protective measures are introduced.
Organizational protective measures refer to changes in the organization of work or processes in order to reduce risks for employees. They include internal regulations such as operating instructions, training, workplace rotations and the implementation of clear work instructions.
Their aim is to design working conditions and practices in such a way that they are safer and enable employees to identify and minimize risks.
3. personal measures (P):
Personal measures are considered as a last resort.
Personal protective measures are special equipment or precautions provided to employees to protect themselves from hazards.
These could include safety helmets, safety goggles, safety shoes or hearing protection. They are the last line of defence if technical and organizational measures are not sufficient or cannot be implemented.
Despite their importance, personal measures should not be seen as the main solution, but as additional protection to be used in conjunction with other protective measures.
The selected protective measures are then implemented - they can include measures such as the provision of special equipment, employee training or the use of a personal emergency signal system.
Conclusion: Risk assessment as the cornerstone of occupational health and safety
Risk assessment is of fundamental importance in the working environment as it serves as an effective tool for identifying, evaluating and controlling potential hazards and risks in the workplace.
Their importance is not only due to their function as a central element of the legal requirements under the Occupational Health and Safety Act (ArbSchG), but is based above all on their fundamental contribution to protecting the health and safety of employees.
The systematic analysis and evaluation of hazards as part of the risk assessment makes it possible to identify accidents, injuries and health risks in the workplace and to take appropriate protective measures.
As a result, preventive measures are developed and implemented to minimize or eliminate potential risks.
The targeted approach to risk assessment helps to make workplaces safer and protect the health of employees.
The risk assessment therefore acts as the cornerstone for creating a safe working environment that not only complies with legal regulations, but also ensures the well-being and safety of the workforce.
Their ongoing application and regular updating are crucial in order to respond appropriately to changing working conditions and new risks and thus establish a sustainable safety culture in the workplace.